Preventing corrosion and wear in chemical valves is crucial for maintaining their performance and integrity over time. Here are some measures that are commonly implemented:
Material Selection: Engage in a thorough materials analysis, considering not only the immediate contact with the process fluid but also potential exposure to atmospheric conditions. Collaborate with metallurgists and materials scientists to understand the microstructural nuances of alloys. Explore the benefits of alloy additions like molybdenum or nickel for enhanced corrosion resistance. Consider specialized treatments such as passivation to fortify the material against chemical attack.
Coatings and Linings: Enter a meticulous process of coating selection by evaluating parameters like adhesion strength, thickness uniformity, and chemical inertness. Explore advanced coating technologies such as plasma spraying or chemical vapor deposition for a precise and durable application. Consider the application of dual-layer coatings for added resilience against abrasion and erosion. Integrate sacrificial coatings that can be easily replenished during maintenance intervals.
Regular Inspection and Maintenance: Establish a multifaceted inspection regimen that includes not only visual assessments but also advanced techniques like phased-array ultrasonic testing and eddy current inspections. Implement an integrated maintenance management system that uses data analytics to predict failure trends and optimize downtime. Incorporate robotic inspection tools for internal examinations, reducing the need for valve disassembly.
Cathodic Protection: Dive into the complexities of cathodic protection design, considering factors like soil resistivity, current distribution, and coating quality. Employ advanced modeling software to simulate the effectiveness of various cathodic protection strategies under dynamic conditions. Utilize remote monitoring systems that provide real-time data on the effectiveness of sacrificial anodes or impressed current systems, allowing for immediate adjustments.
Corrosion Inhibitors: Contribute to the development of custom corrosion inhibitor formulations tailored to the specific chemical composition of the process fluid. Explore nanotechnology applications for inhibitor delivery, ensuring a controlled and sustained release. Implement an autonomous monitoring system that employs sensors and machine learning algorithms to dynamically adjust inhibitor dosages based on real-time corrosion rates.
Proper Installation: Elevate the precision of valve installation by employing laser alignment technologies with sub-millimeter accuracy. Integrate real-time stress analysis tools to identify potential stress concentration points during installation. Collaborate with 3D modeling experts to simulate installation scenarios and optimize procedures, ensuring uniform loading across the valve components.
Sealing Systems: Embark on a comprehensive review of seal materials, examining not only their chemical resistance but also their resilience under dynamic conditions. Employ finite element analysis to simulate seal performance under various pressures and temperatures. Implement real-time seal monitoring systems that provide feedback on compression set and wear, enabling predictive maintenance interventions.
Avoidance of Galvanic Corrosion: Undertake an exhaustive galvanic corrosion risk assessment, considering parameters such as surface area ratios and electrochemical potentials. Deploy advanced sensors that continuously monitor galvanic coupling effects, providing early warnings of potential corrosion. Integrate smart systems that automatically adjust impressed current levels or sacrificial anode compositions based on real-time galvanic corrosion assessments.
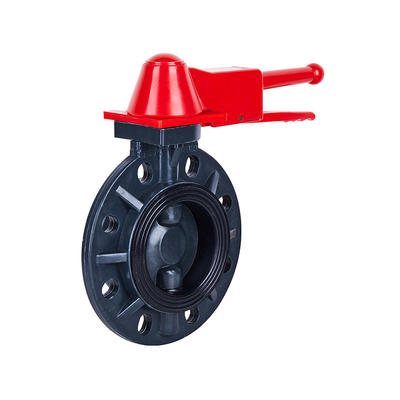
The valve is small and light, easy to disassemble and repair, and can be installedat any position.
The structure is simple & compact, and the operating torque is small, and the 90° rotation is opened quickly.
The flow characteristics tend to be straight and the adjustment performance is good