To ensure the long-term functionality of PVDF valves, it is essential to follow proper maintenance and servicing practices. Here are some recommendations:
1.Regular Inspection:
Conduct routine visual inspections of PVDF valves to detect any signs of wear, corrosion, or mechanical damage. Utilize magnification tools if necessary to inspect intricate parts thoroughly. Document and analyze any anomalies observed during inspections.
2.Cleaning:
Implement a scheduled cleaning regimen using mild, non-abrasive cleaning agents compatible with PVDF material. Avoid harsh chemicals that might degrade the valve components. Use proper cleaning tools to reach recessed areas, ensuring the removal of all contaminants.
3.Lubrication:
Apply lubricants specifically formulated for PVDF valves to moving parts, ensuring smooth operation and minimal friction. Regularly assess the lubrication levels and reapply as needed. Over-lubrication should be avoided, as it can attract dust and debris, potentially hindering the valve's functionality.
4.Seal Inspection:
Routinely inspect seals and gaskets for signs of wear, distortion, or chemical degradation. Damaged seals can compromise the integrity of the valve, leading to leaks and inefficiencies. Promptly replace worn-out seals with high-quality, compatible replacements sourced from the valve manufacturer or authorized suppliers.
5.Pressure and Temperature Monitoring:
Continuously monitor operating parameters, such as pressure and temperature, within the prescribed limits. Deviations from specified ranges can adversely affect the valve's performance and compromise its longevity. Implement real-time monitoring systems to promptly detect and address fluctuations.
6.Actuator Maintenance:
If the PVDF valve incorporates an actuator, conduct regular maintenance checks on the actuator assembly. Verify its responsiveness to control signals, inspect electrical connections, and calibrate as necessary. Address any actuator-related issues promptly to ensure precise valve control.
7.Corrosion Prevention:
While PVDF valves are inherently resistant to corrosion, monitor the surrounding environment to prevent exposure to corrosive substances. Implement protective measures, such as coatings or enclosures, if the valve is situated in an environment prone to chemical exposure or corrosive elements.
8.Training and Awareness:
Provide comprehensive training to personnel responsible for operating and maintaining PVDF valves. Ensure that they are well-versed in the specific requirements of PVDF valves, including proper handling, maintenance protocols, and safety precautions. Regular training updates can reinforce best practices.
9.Documentation:
Maintain meticulous records of all maintenance activities, including inspection dates, cleaning procedures, parts replacements, and repairs. Organized documentation facilitates historical tracking of the valve's performance, aiding in predictive maintenance strategies and decision-making processes.
10.Spare Parts Inventory:
Maintain a strategic inventory of essential spare parts, including seals, gaskets, O-rings, and actuator components. Regularly assess the inventory levels and restock items to avoid delays in replacements. Collaborate with suppliers to ensure a seamless supply chain for spare parts.
11.Professional Servicing:
Engage qualified technicians or engineers experienced in PVDF valve systems for complex issues or preventive maintenance tasks. Professional servicing should adhere to industry standards and manufacturer recommendations. Regularly scheduled professional inspections can uncover potential problems before they escalate.
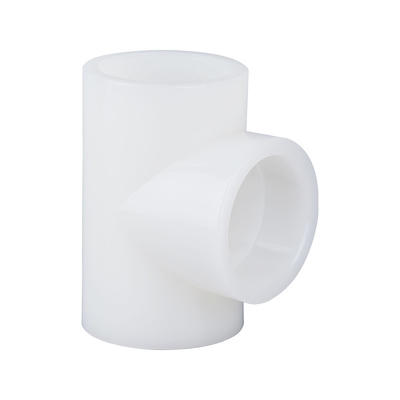
Material: CPVCColour: Gray
Technics: Forged
Connection: socket
Shape: Equal
Head Code: Square
Color: Gray
Size: DN15-DN600
Application: Industry