A PVDF Valve can be used in applications where high-performance temperature control is necessary, especially for packaging type applications. The reason is that PVDF is a solid rather than hollow plastic, which allows it to have a superior thermal conductivity to a variety of inks and solvents. The thermosetting performance is excellent, especially with a ball valve. Pipe valves manufactured out of PVDF deliver an optimal thermal performance range well over 284 degrees F to thermally regulate fluids such as Freon and kerosene. PVDF valves also offer extensive chemical resistance even to some of the most extreme solutions including highly concentrated sulfuric acid and even hot molten metal.
Apart from the low temperature and high resistance features, another key advantage of using PVC materials is that they can be applied in such a way as to prevent air leakage. For example, a PVC pipe may be tied closed using PVC glue, resulting in a seal that prevents contaminants entering the flange end of the pipe. Other seals include polyethylene packing tape and other forms of sealing tape. All these forms of sealing, if combined together with high performance PVDF valve fixtures can completely eliminate the need for sealing altogether, and thus cut down on installation costs for a variety of packaging types.
Because polyvinyl chloride (PVC) is thermally broken down into its component molecules when pressure is applied, the liquid or gas flowing through it develops "thermal turbulence." In effect, the liquid or gas varies the pressure within the pipes as it negotiates through the valve's flange end. Since PVDF does not have any melting points, this process of thermal turbulence is inherent in all types of PVC valves, regardless of their application. Additionally, the thermal resistance extends not only to the valve but also to the packaging, which is the source of the valve's physical form and function.
When manufacturing PVC seals, skilled craftsmanship is the only thing that limits the application of these valves. The ability to match the valve to the packaging type as well as the flow function and pipe diameter, and then match the PVDF valve to the specific packaging type is a specialized skill set that not all manufacturers possess. The ability to work with intricate detail, coupled with a sharp production vision, can result in exceptionally accurate valve shapes and sizes, as well as a correspondingly optimized valve assembly.
From a design perspective, the PVDF manufacturing process begins with a molding machine. Once the desired shape and size of the valve is finalized, it is transferred to a plastic sheet that has been specially printed for this purpose. This printing process is necessary because the printed sheet must be perfectly straight and flat in order to accept the entire valve as it is seamlessly fitted into the end hole. Once this operation is complete, the valve is then ready to be tested in a variety of conditions, which involves thoroughly loosening the bolt and preparing the casting lever for its final insertion into the valve hole.
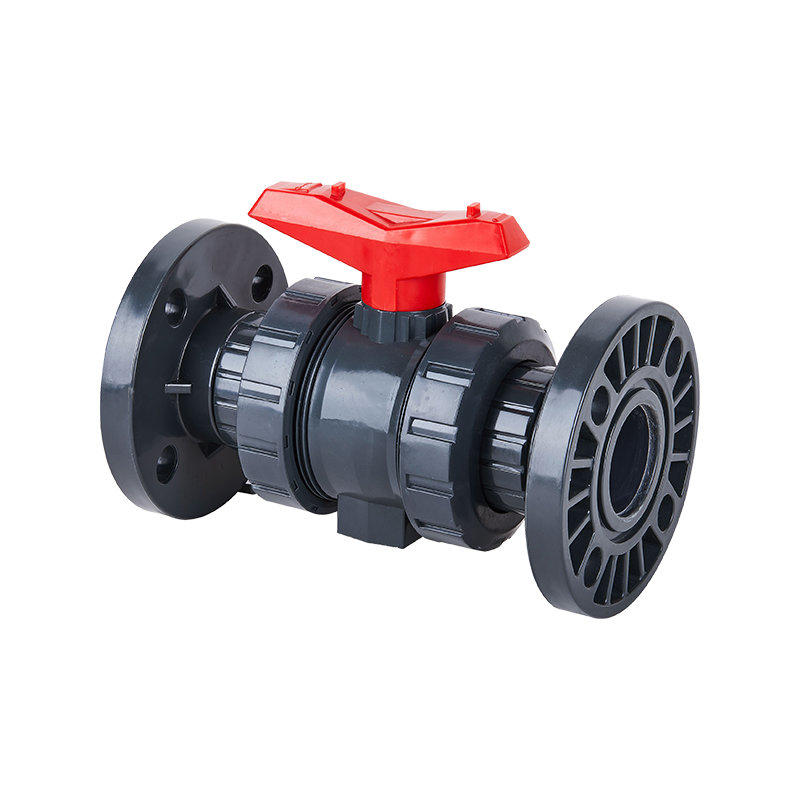