Industrial valves regulate fluid flow in piping systems. They are either manually operated or equipped with an actuator that changes the valve's opening and closing conditions. This is a key aspect of valve selection for the chemical processing industry, as valves can represent a significant part of the system's overall expenditure. However, if a valve is incompatible with the system it controls, the resulting flow can be hazardous and potentially unsafe.
Bubble-tight valves are used when regulating flow rates. This type of valve works well for liquids with a high degree of viscosity, such as those with solid matter suspended in them. These valves are often used in throttling systems, as well as for the transmission of semi-solids. They are also available with a wafer or lug end construction, depending on the application. Industrial valves can be purchased at reasonable prices, so you won't have to compromise quality for cost.
Choosing a valve with stainless steel construction is a great choice if you're working in an environment with corrosive media. For high-pressure, high-temperature applications, and strict sanitation standards, stainless steel valves are a good choice. Choosing a valve made of non-sparking materials is recommended for processing solvents, fuels, and volatile organic compounds (VOCs). It's also important to check the chemical compatibility of internal trim parts, including elastomers.
For more precision, ball valves are another good choice. Their hollow middle allows them to control flow with extreme precision. When closed, they have a bore that matches the pipeline. Rotating the ball 90 degrees allows them to restrict the flow, and the walls of the ball are parallel to the pipeline. Normally, the bore size of a ball valve is equal to or slightly smaller than the diameter of the pipeline. However, in large sizes, double stems are necessary to accommodate larger fluids.
Pipeline fittings and valves are necessary for the transport of waste fluids and valuable resources. Oil and gas pipelines use durable fittings to prevent dangerous pressure conditions. And, of course, manufacturing is another industry that relies on piping systems to control process fluids. Industrial valve pipe, check valves, and iron gates are among the most common types of fittings. For more information, visit Boyd Metals' Pipe Sizes Guide to make your selection easier.
Once you've determined the flow rate and sizing of your Industrial Valve Pipe, it's time to choose the type of end connection. Some valves have multiple end connections, while others only have one. Your decision on valve end connection is critical for both its performance and the safety of the system. Therefore, choosing the proper size is essential to ensure safe, accurate, and reliable operation. Remember that the proper pipe size determines the performance of the valve and its cost.
If your Industrial Valve Pipe fails, your production operations could be interrupted. An inoperable valve may allow hazardous chemicals to mix with airborne toxins. And, in the worst case scenario, a failed valve may result in a disastrous spill. Inadvertent mixtures can also result in deadly byproducts and accelerate the wearing of the pipes. You may need to shut down the entire plant to repair just one valve.
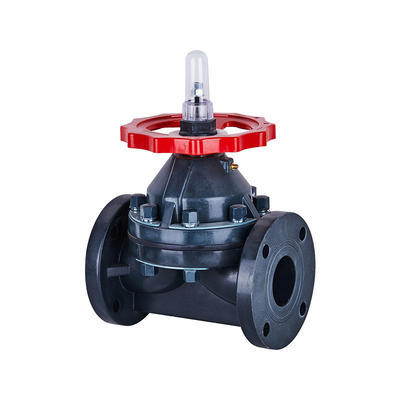