When facing a failure or malfunction with an FRPP (Fluorinated Polypropylene) plastic pipe valve, users can follow a series of troubleshooting steps to identify and address the issue. Here are some general guidelines:
Check for Visual Signs of Damage: Utilize non-destructive testing methods such as dye penetrant inspection or magnetic particle testing for a comprehensive examination of the valve's structural integrity.
Investigate the surface finish for any signs of discoloration or irregularities, which may indicate localized overheating or chemical reactions.
Consider employing thermal imaging to identify temperature differentials across the valve, providing insights into potential stress points.
Review Operating Conditions: Utilize data loggers and trend analysis tools to assess historical operating conditions, identifying trends or abnormalities leading up to the malfunction.
Employ computational fluid dynamics (CFD) simulations to model fluid flow within the valve under different conditions, helping to predict potential failure points.
Investigate the impact of transient conditions, such as sudden pressure spikes, on the valve's mechanical behavior.
Inspect Seals and Gaskets: Conduct a microscopic examination of seals and gaskets to identify microscopic wear patterns or material fatigue.
Implement Fourier-transform infrared (FTIR) spectroscopy to analyze molecular changes in the seals, providing insights into chemical degradation.
Utilize a hardness tester to assess the durometer of elastomeric seals, ensuring they meet specified hardness requirements.
Examine Valve Actuation: Disassemble the actuator to inspect internal components, utilizing precision measuring instruments to assess gear wear and tolerances.
Employ vibration analysis tools to identify resonances or abnormal vibrations during actuation, indicative of mechanical issues.
Consider employing strain gauges on critical actuator components to monitor and analyze stress distribution during operation.
Evaluate Fluid Compatibility: Conduct accelerated aging tests on FRPP samples immersed in the target fluid to simulate long-term exposure effects.
Employ scanning electron microscopy (SEM) to analyze the molecular structure of FRPP after exposure to the fluid, revealing microscopic changes.
Collaborate with material scientists to conduct comprehensive chemical compatibility tests under varying temperature and pressure conditions.
Check for Blockages: Utilize computational fluid dynamics simulations to model flow patterns within the valve and identify potential areas of stagnation or blockage.
Implement advanced inspection tools such as endoscopes with articulating tips to navigate complex geometries and locate hidden blockages.
Conduct ultrasonic thickness measurements on piping walls to identify potential buildup of deposits that may lead to blockages.
Review Control System: Utilize oscilloscopes to analyze control signals, identifying signal quality, latency, or voltage irregularities.
Implement advanced diagnostic tools such as signal analyzers to detect electromagnetic interference or other disturbances affecting the control system.
Collaborate with control system engineers to conduct a failure mode analysis on the control system components, including sensors, actuators, and communication interfaces.
Monitor Valve Position Indication: Implement laser interferometry to achieve highly precise measurements of valve position, ensuring accurate verification of position indicators.
Employ redundancy in position sensing mechanisms, such as dual sensors or redundant position indicators, to enhance reliability.
Utilize advanced telemetry systems to remotely monitor and record valve position data over extended periods for trend analysis.
Perform Leak Tests: Employ tracer gas leak detection methods for ultra-sensitive leak identification, complemented by mass spectrometry for quantitative analysis.
Conduct pressure decay tests with high-precision pressure transducers to quantify the rate of leakage and identify potential intermittent leaks.
Utilize thermal imaging cameras to detect temperature anomalies caused by escaping fluids, aiding in pinpointing elusive leaks.
FRPP Male Couping Adapter DN15-50
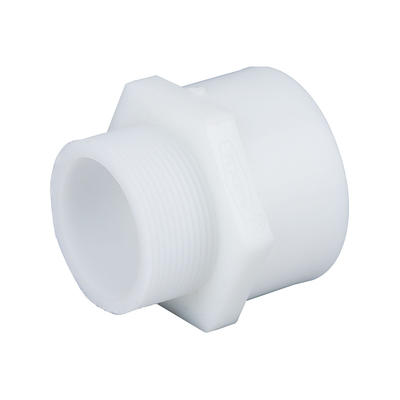
FRPP Male Couping Adapter DN15-50
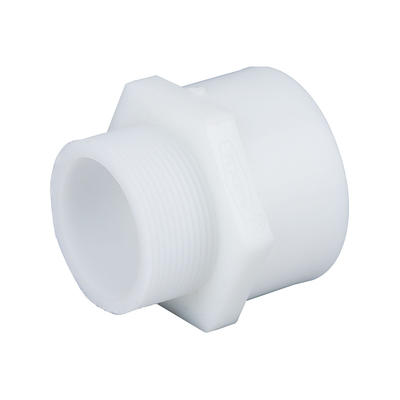