The operating temperature and pressure range of a chemical valve are critical factors that significantly impact its performance and longevity. Here's a breakdown of their influence:
1.Material Integrity:
Temperature: Extreme temperatures can significantly impact the structural integrity of the materials used in chemical valves. High temperatures induce thermal expansion, potentially causing dimensional changes and stressing the material. Conversely, low temperatures can render materials brittle, increasing the likelihood of fractures. Selecting materials with appropriate coefficients of thermal expansion is crucial to maintain dimensional stability across the operational temperature range.
Pressure: Elevated pressure levels expose valve materials to heightened mechanical stress. The chosen material must possess sufficient strength and durability to withstand the mechanical stress induced by high pressure without undergoing deformation or failure. Similarly, materials should retain their structural integrity under low-pressure conditions to prevent material fatigue and degradation.
2.Sealing Performance:
Temperature: Seals and gaskets, integral to chemical valves, are highly susceptible to temperature variations. Temperature changes can impact the elasticity and hardness of these sealing elements, directly influencing their ability to maintain a consistent and effective seal. Optimal sealing performance demands the selection of materials that exhibit stable mechanical properties across the entire temperature range.
Pressure: Seals must not only resist mechanical stress induced by pressure but also maintain their sealing integrity under varying pressure differentials. High pressure can compress seals, compromising their effectiveness and leading to potential leaks. Therefore, robust seal design and careful material selection are imperative to withstand pressure-related challenges.
3.Fluid Characteristics:
Temperature: Chemical reactions and alterations in fluid viscosity often exhibit temperature-dependent behavior. The temperature range of a chemical valve should align with anticipated variations in fluid characteristics. A thorough understanding of how temperature influences chemical processes is crucial for selecting a valve capable of effectively controlling and modulating fluid flow under diverse temperature conditions.
Pressure: Elevated pressure can modify the behavior of chemicals, increasing their corrosiveness or reactivity. Valve materials and designs must account for potential changes in chemical properties induced by pressure, ensuring compatibility and longevity in reactive environments.
4.Mechanical Stress:
Temperature: Thermal expansion and contraction can subject valve components, particularly moving parts like stems and actuation mechanisms, to mechanical stress. This stress may lead to material fatigue, compromising the overall functionality of the valve. Therefore, careful consideration of material properties and the incorporation of appropriate design measures, such as expansion joints, are necessary to mitigate thermal-induced mechanical stress.
Pressure: Cyclic loading on moving parts due to pressure fluctuations can result in fatigue failure. Robust design, material selection, and, if applicable, periodic maintenance practices are crucial to minimizing the impact of pressure-induced mechanical stress on valve components.
5.Thermal Expansion:
Temperature: Valve components may experience thermal expansion or contraction at different rates, causing dimensional changes. This can affect the overall dimensional stability of the valve, impacting alignment and sealing capabilities. Selecting materials with compatible thermal expansion coefficients and employing engineering techniques, such as thermal insulation or expansion joints, can effectively manage thermal effects and maintain dimensional stability.
Pressure: Changes in pressure can exacerbate thermal expansion effects, necessitating a holistic approach to valve design. This involves selecting materials that can accommodate both thermal and pressure-induced dimensional changes without compromising the structural integrity of the valve.
UPVC Type B Socket Ball Valve DN15-100
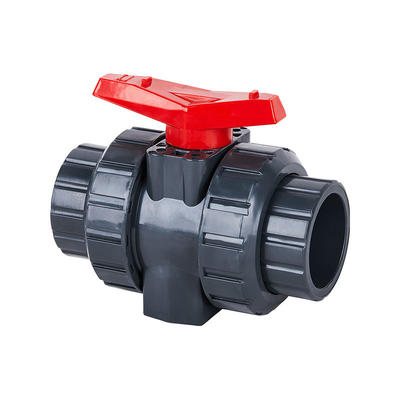
UPVC Type B Socket Ball Valve DN15-100
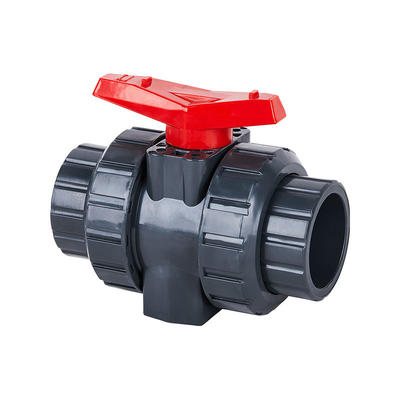