The ability of a corrosion-resistant plastic centrifugal pump to handle temperature variations in corrosive environments depends on several factors:
Thermal Expansion: Corrosion-resistant plastics feature significantly lower coefficients of thermal expansion compared to metals, mitigating the risk of dimensional changes and mechanical stresses induced by temperature fluctuations. For instance, the coefficient of thermal expansion for polypropylene is approximately 70-100 x 10^-6 /°C, much lower than that of metals like stainless steel (approximately 16.3 x 10^-6 /°C). This inherent property minimizes the likelihood of warping, distortion, or cracking in plastic pump components subjected to thermal cycling, preserving dimensional accuracy and structural integrity over time.
Design Considerations: The design of a corrosion-resistant plastic centrifugal pump incorporates various features to accommodate thermal expansion and contraction effectively. Structural components are engineered with ample clearance and tolerance to prevent binding or interference during temperature variations. Flexible connections, such as rubber or elastomeric seals, compensate for thermal movements without imposing undue stress on the pump assembly. Geometric optimizations, such as ribbing or reinforcement, enhance the rigidity and stability of critical components, reducing susceptibility to thermal deformation and fatigue failure under cyclic thermal loading.
Cooling Systems: In applications where temperature fluctuations pose significant challenges, supplementary cooling systems may be integrated to regulate the thermal environment surrounding the pump. External cooling jackets, fabricated from materials compatible with corrosive fluids, dissipate excess heat generated during operation, maintaining the pump within its designated temperature range. Cooling coils embedded within the pump housing facilitate efficient heat exchange, facilitating rapid temperature stabilization and preventing overheating-induced damage. Heat exchangers, utilizing coolant fluids or air, provide an additional layer of thermal control, enhancing the pump's resilience to temperature variations and extending its operational lifespan in aggressive chemical environments.
Insulation: Thermal insulation plays a pivotal role in minimizing heat transfer and stabilizing internal temperatures within the pump system, thereby safeguarding against temperature fluctuations and thermal shock. Insulating materials, such as foamed plastics, ceramic fibers, or elastomeric coatings, create a thermal barrier that reduces heat losses and maintains consistent operating conditions. Proper insulation not only protects the pump from external temperature variations but also optimizes energy efficiency by minimizing thermal inefficiencies associated with heat transfer across piping and equipment surfaces. By mitigating temperature gradients and thermal stresses, insulation enhances the long-term reliability and performance of the pump in corrosive environments.
Monitoring and Control: Robust temperature monitoring and control systems are instrumental in ensuring the safe and reliable operation of the pump amidst temperature variations. Advanced temperature sensors, strategically positioned at critical locations within the pump assembly, continuously monitor thermal conditions, providing real-time data on temperature fluctuations and trends. Automated control systems, equipped with sophisticated algorithms and feedback mechanisms, regulate pump operation to maintain temperatures within predetermined limits, optimizing performance and efficiency while mitigating the risk of thermal damage or operational anomalies. Integrated alarm systems and emergency shutdown protocols offer fail-safe mechanisms to respond promptly to overheating events or temperature-related abnormalities, minimizing downtime and safeguarding personnel and assets from potential hazards associated with thermal instability.
FP Direct Type Centrifugal Pump
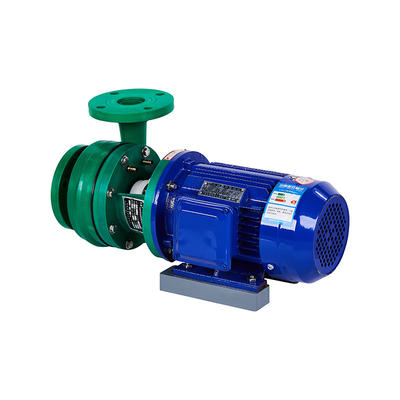
FP Direct Type Centrifugal Pump
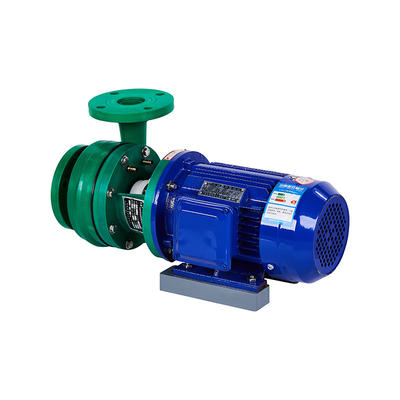