The chemical resistance and compatibility of plastic materials in valve applications play a crucial role in determining the performance and reliability of the valves in practice. Here's how Chemical Plastic Valves Pipe Suppliers reflects:
1. Material Testing and Selection: In practice, extensive testing is conducted to evaluate the chemical resistance of different plastic materials. This involves exposing the materials to various chemicals and measuring their performance, such as dimensional stability, strength, and resistance to degradation. Based on the test results and the specific requirements of the application, engineers can select the most suitable plastic material that exhibits excellent chemical resistance and compatibility.
2. Performance in Harsh Environments: Valves are often used in demanding environments where they may come into contact with aggressive chemicals, high temperatures, or extreme pressures. Plastic materials with superior chemical resistance are chosen to withstand these harsh conditions. They can resist chemical attack, maintain their mechanical properties, and ensure reliable operation over extended periods.
3. Compatibility with Multiple Chemicals: In many cases, valves are required to handle different types of chemicals or fluids. Plastic materials with broad chemical compatibility are preferred to ensure the valves can handle a wide range of substances without degradation or failure. This versatility allows the valves to be used in various industrial applications, such as chemical processing, water treatment, pharmaceuticals, and oil and gas.
4. Resistance to Corrosion and Erosion: Chemical resistance is vital in preventing corrosion and erosion of valve components. When plastic materials are resistant to the chemicals they encounter, they remain structurally sound, preventing deterioration and maintaining the integrity of the valve. This resistance helps to avoid leaks, prolong the lifespan of the valve, and minimize the need for frequent maintenance or replacement.
5. Material Durability and Longevity: The chemical resistance and compatibility of plastic materials directly impact the durability and longevity of valves. When the materials can withstand the specific chemicals and fluids involved, they exhibit prolonged service life, reducing downtime and replacement costs. This is particularly important in critical applications where reliability and continuous operation are essential.
6. Compliance with Industry Standards: Various industries have specific standards and regulations regarding chemical resistance and compatibility in valve applications. Manufacturers ensure that the selected plastic materials meet these standards to ensure safety, reliability, and compliance with environmental regulations. This includes considering factors such as resistance to specific chemicals, temperature limits, pressure ratings, and long-term performance.
7. Ongoing Monitoring and Maintenance: While plastic materials may exhibit excellent chemical resistance initially, it is crucial to monitor their performance over time. Regular inspections and maintenance help identify any signs of degradation or reduced chemical resistance. This proactive approach allows for timely repairs or replacements, ensuring the continued reliability and safety of the valves.
Proper material selection, testing, and ongoing monitoring are essential to ensure that the chosen plastic materials can withstand the specific chemicals and conditions they will encounter, providing long-term durability and effective operation in various industries.
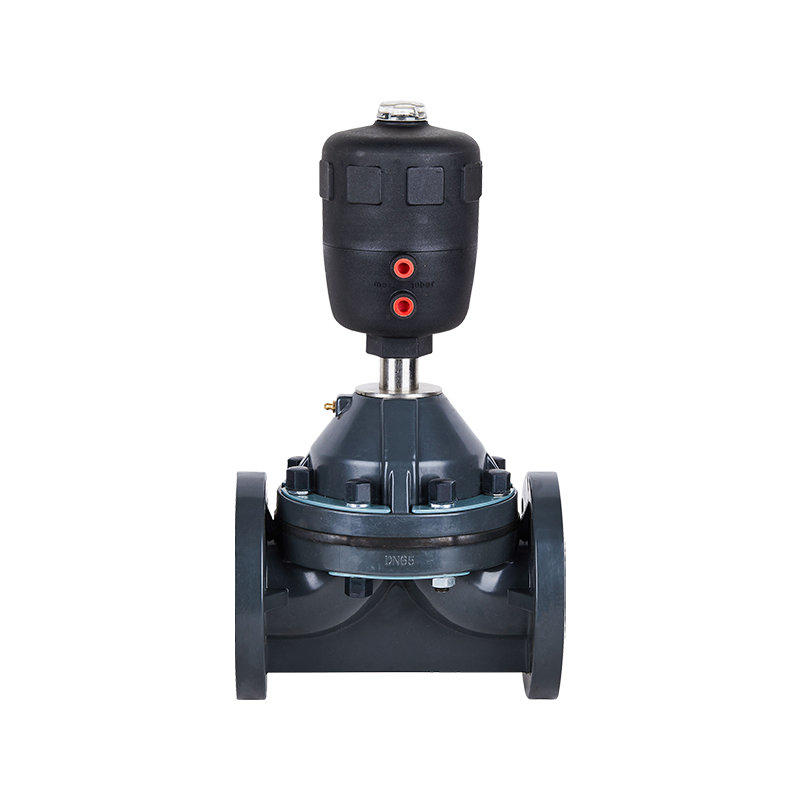
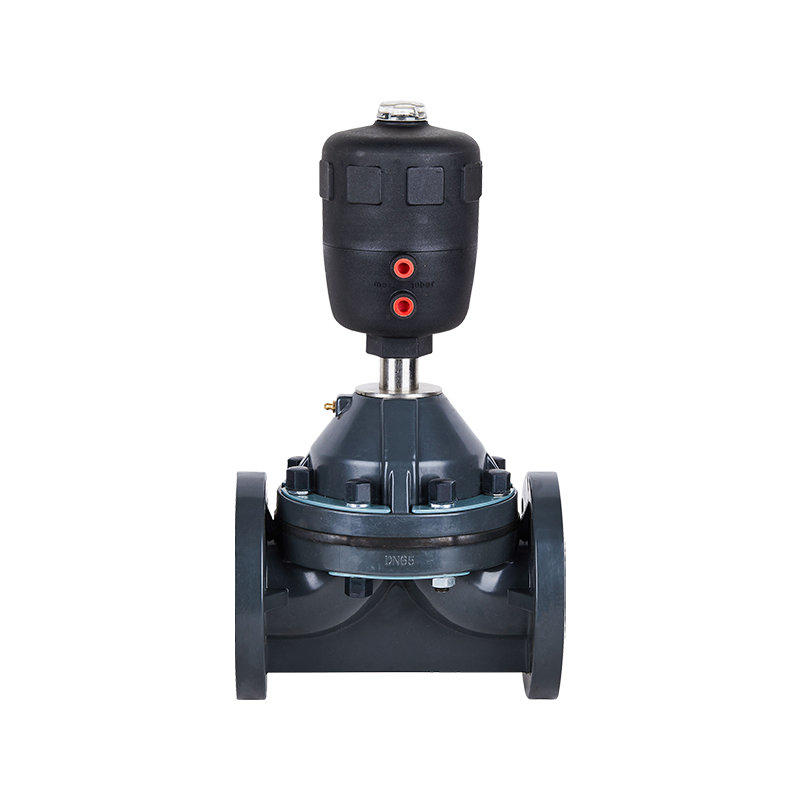
1.The seal diaphragm is made of F46 or PFA,the number of folds is ≥120000 times,and the corrosion resistance is equivalent to F4.
2.Adopting the screw lifting structure,the opening and closing force is huge and the stability is good.