Environmental factors such as humidity and exposure to corrosive gases can significantly impact the corrosion resistance of plastic pumps. Here's an explanation of their influence and precautions users should take:
1.Humidity:
Influence: Elevated humidity levels can introduce challenges for plastic pump components, as certain plastics may absorb moisture, potentially compromising their mechanical properties. This absorption can lead to dimensional changes and affect the overall performance of the pump.
Precautions: Choose plastic materials with low water absorption rates, such as those with hydrophobic characteristics.
Implement stringent storage conditions, ensuring that the pump is stored in a dry environment with controlled humidity levels.
Conduct regular material testing to assess the impact of humidity on mechanical properties and adjust maintenance schedules accordingly.
2.Exposure to Corrosive Gases:
Influence: Corrosive gases in the environment can chemically attack plastic pump materials, leading to degradation and reduced corrosion resistance. Understanding the specific gases present is crucial for selecting suitable materials.
Precautions:Employ gas detection systems in the operating environment to monitor concentrations and identify potential risks.
Periodically review and update material selection based on evolving environmental conditions and gas compositions.
3.Material Compatibility:
Influence: The choice of plastic material significantly influences its response to environmental factors. Optimal material selection is crucial to ensure prolonged corrosion resistance in the presence of humidity and corrosive gases.
Precautions: Conduct comprehensive material compatibility studies, simulating real-world conditions to assess the long-term impact on the plastic pump components.
Engage with material suppliers to stay informed about advancements in corrosion-resistant plastics and adopt newer, more resilient materials as appropriate.
4.Surface Protection:
Influence: Corrosive gases can accelerate surface degradation, emphasizing the need for protective measures. Coatings or finishes act as an additional barrier, enhancing the overall corrosion resistance of plastic pumps.
Precautions: Employ corrosion-resistant coatings that are specifically designed for the intended operating environment.
Regularly inspect and maintain coatings, ensuring they remain intact and effective against corrosive elements.
Consider periodic recoating based on environmental conditions and the wear pattern observed during inspections.
5.Regular Inspection and Maintenance:
Influence: Humidity and corrosive gases can contribute to gradual wear or damage. Regular inspection and maintenance routines are essential to detect issues early, preventing potential failures and ensuring continuous pump performance.
Precautions: Develop a comprehensive inspection checklist covering all critical components, including seals, gaskets, impellers, and structural elements.
Implement non-destructive testing methods to assess the integrity of plastic components.
Establish clear protocols for addressing identified issues promptly and comprehensively.
6.Climate-Controlled Storage:
Influence: Improper storage conditions, particularly in high humidity environments, can impact the condition of the pump before installation, potentially leading to premature degradation.
Precautions: Store plastic pumps in controlled environments with stable temperature and humidity levels, adhering to manufacturer recommendations.
Utilize protective packaging and covers to shield pumps from environmental elements during storage.
Implement a rigorous receiving inspection process to assess the condition of pumps upon delivery and identify any issues arising from storage.
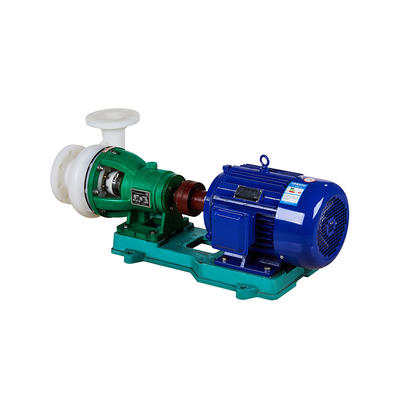
Application: wastewater treatment, Chemical
Pressure: custom, High Pressure
Structure: Direct Type Centrifugal Pump
Outlet Size: custom
Power: Electric