There are several safety considerations when working with PVC valves, especially in high-pressure systems. Here are some key points to keep in mind:
1.Pressure Ratings: PVC valves come with specified pressure ratings, indicating the maximum pressure they can safely handle. It is imperative to choose valves that are rated for the system's operating pressure. Using a valve with a lower pressure rating than the system pressure can lead to catastrophic failure, causing leaks or bursts, posing serious risks to personnel and equipment integrity.
2.Temperature Limits: PVC valves have defined temperature limits within which they can operate effectively. Operating the valves beyond these limits can result in the material becoming brittle or losing structural integrity. This can lead to cracking or rupturing of the valve, causing significant safety hazards. Always refer to the manufacturer's specifications to ensure the valves are used within the designated temperature range.
3.Chemical Compatibility: PVC valves are resistant to many chemicals, but not all. It is crucial to verify the compatibility of the valve material with the fluids or gases in the system. Exposure to incompatible substances can cause the PVC to deteriorate, leading to failure. Conduct a thorough chemical compatibility analysis to prevent corrosive reactions that could compromise the integrity of the valve and the overall system.
4.Proper Installation: Correct installation practices are fundamental for the safe operation of PVC valves. Follow the manufacturer's guidelines meticulously. This includes using the appropriate solvent cement, ensuring proper alignment and seating of the valve, and employing the correct threading techniques. Inadequate installation can result in leaks, structural stress, or misalignment, all of which can jeopardize the safety of the system.
5.Avoiding Impact and Stress: PVC valves are susceptible to damage from physical impact or stress. Avoid dropping or hitting the valves during transportation, storage, or installation. Additionally, be mindful of stress concentrations, such as excessive torque during threading, which can lead to cracks or fractures. Proper handling and care are essential to prevent structural damage to the valves.
6.Regular Inspection: Implement a regular inspection schedule for PVC valves. Visual inspections should include checking for signs of wear, corrosion, or any visible damage. Leaks, discoloration, or deformation are indicators of potential issues. Any compromised valves should be replaced immediately to maintain system integrity and prevent accidents.
7.Pressure Relief: In high-pressure systems, install pressure relief devices strategically. Pressure relief valves are essential components that automatically release excess pressure if it exceeds safe levels. Properly sized and maintained relief valves can prevent over-pressurization, offering a crucial safety measure and protecting the system from potential failures.
8.Training and Awareness: Ensure that personnel working with PVC valves are well-trained and fully aware of the safety protocols. Training should encompass proper handling, installation techniques, and emergency procedures. Awareness of potential hazards and the correct response in case of a valve failure is vital to maintaining a safe working environment.
9.Emergency Response: Develop a comprehensive emergency response plan that outlines clear procedures for shutting down the system, containing leaks, and evacuating personnel if required. Personnel should be trained in executing these protocols efficiently to minimize risks in the event of a PVC valve failure.
FRPP Van Stone Flange DN15-600
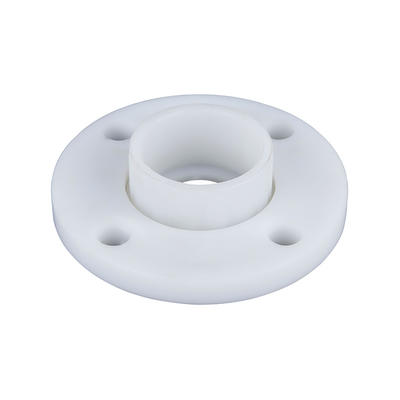
FRPP Van Stone Flange DN15-600
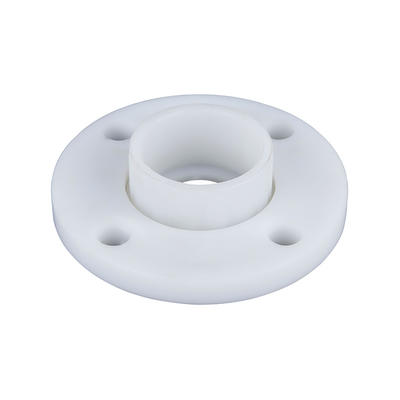