Choose good valve
It is essential for the long-term operation of the device under working conditions
The importance of valve selection
Nowadays, there are more and more valves on the market, the types of valves are particularly complex, and the structures and materials are all different. The selection of the valve is very important for the long-term operation of the device in the working condition. Improper selection of valves and users' ignorance of valves are the source of accidents and safety threats. Nowadays, the demand for valve products in the social industry is becoming more and more extensive, and users should have a further understanding and cognition of knowledge about valves and other aspects.
The following are the dry goods for valve selection ,
If you see it, you must forward it and collect it~
First, the key points of valve selection
1. Correctly choose the type of valve
The correct choice of valve type is based on the designer's full grasp of the entire production process and operating conditions as a prerequisite. When selecting the valve type, the designer should first grasp the structural characteristics and performance of each valve.
2. Clarify the purpose of the valve in the equipment or device
Determine the working conditions of the valve: the nature of the applicable medium, the working pressure, the working temperature and the control method of operation, etc.
3. Selection of valve material
When selecting the material of the valve's shell, internal parts and sealing surface, in addition to considering the physical properties (temperature, pressure) and chemical properties (corrosiveness) of the working medium, the cleanliness of the medium (with or without solid particles) should also be grasped. In addition, it is necessary to refer to the relevant regulations of the country and the user department.
The correct and reasonable selection of the valve material can obtain the most economical service life and the best performance of the valve.
4. Determine the end connection of the valve
Among threaded connections, flange connections, and welded end connections, the first two are the most commonly used. Threaded valves are mainly valves with a nominal diameter below 50mm. If the diameter is too large, it will be very difficult to install and seal the connection.
Flange-connected valves are easier to install and disassemble, but they are heavier and more expensive than screw-connected valves, so they are suitable for pipe connections of various diameters and pressures.
Welding connection is suitable for harsher conditions and is more reliable than flange connection. However, it is more difficult to disassemble and reinstall the valve connected by welding, so its use is limited to the occasions that can usually operate reliably for a long time, or where the use conditions are harsh and the temperature is high.
5. Other
In addition, the flow rate and pressure level of the fluid flowing through the valve should also be determined, and the appropriate valve should be selected using existing information (such as valve product catalogs, valve product samples, etc.).
2. Valve selection basis
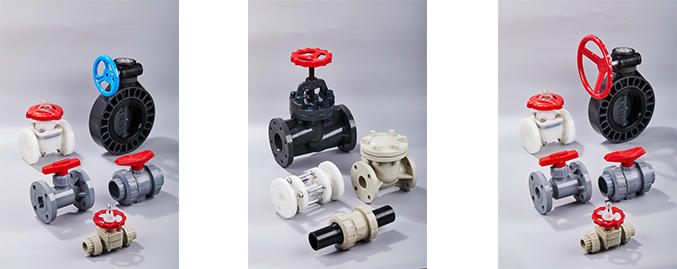
1. Fluid working conditions (pressure and temperature)
2. The nature of the fluid (corrosive, etc.)
3. The purpose of selecting the valve (throttling, pressure control, etc.)
Because the valve has a wide range of uses, it also plays a great role. For example, in power plants, valves can control the operation of boilers and steam turbines; in petroleum and chemical production, valves also control the normal operation of all production equipment and technological processes. The same is true in other departments. Nevertheless, the comparison of valves with other products is often overlooked. For example, when installing machinery and equipment, people tend to focus on the main machinery and equipment, such as compressors, high-pressure vessels, boilers, etc.; some are improperly selected. These practices will reduce the overall production efficiency or stop production, or cause various other accidents. Therefore, serious and responsible work must be carried out on the selection, installation and use of valves. Especially for modern industrial production and construction
The following are the principles to be followed when selecting valves:
⑴ The flow path of the valve for shut-off and open medium is a straight-through valve, and its flow resistance is small, and it is usually selected as a valve for shut-off and open medium. The downward closing valve (stop valve, plunger valve) is less used because of its tortuous flow path and higher flow resistance than other valves. Where a higher flow resistance is allowed, a closed valve can be used.
⑵ The valve used to control the flow is usually the valve that is easy to adjust the flow as the control flow. Downward closing valves (such as globe valves) are suitable for this purpose because the size of its seat is proportional to the stroke of the closing member. Rotary valves (plug valves, butterfly valves, ball valves) and flex-body valves (pinch valves, diaphragm valves) can also be used for throttling control, but they are usually only applicable within a limited range of valve diameters. The gate valve uses a disc-shaped gate to cross-cut the circular valve seat opening. It can only control the flow better when it is close to the closed position, so it is usually not used for flow control.
⑶ Valves used for reversing and diversion, according to the needs of reversing and diversion, this kind of valve can have three or more channels. Plug valves and ball valves are more suitable for this purpose. Therefore, most of the valves used for reversing and splitting select one of these valves. However, in some cases, other types of valves can also be used for reversing and shunting as long as two or more valves are properly connected to each other.
⑷ Valves for medium with suspended particles When there are suspended particles in the medium, it is most suitable to use a valve with a wiping effect on the sliding of its closing part along the sealing surface. If the back and forth movement of the closing member to the valve seat is vertical, it may hold particles. Therefore, this valve is only suitable for basic clean media unless the sealing surface material allows particles to be embedded. Ball valves and plug valves have a wiping effect on the sealing surface during the opening and closing process, so they are suitable for use in media with suspended particles. At present, whether in the pipeline system of petroleum, chemical industry, or other industries, valve applications, operating frequencies and services are ever-changing. To control or prevent even minor leaks, the most important and critical equipment is the valve. The ultimate control of the pipeline is the valve. The service and reliable performance of the valve in various fields is unique.
Three, common valve selection instructions
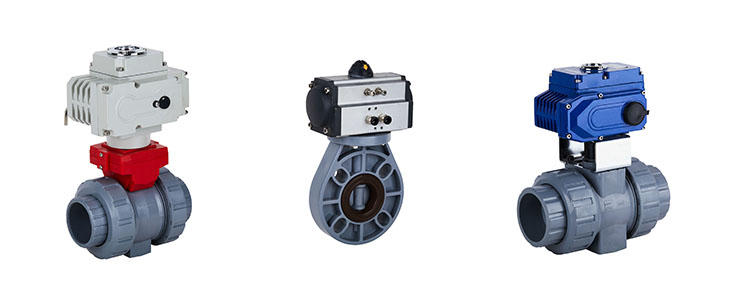
1. Description of ball valve selection
The ball valve is suitable for low-temperature, high-pressure, and high-viscosity media. Most ball valves can be used in media with suspended solid particles, and can also be used in powder and granular media according to the sealing material requirements;
The full-channel ball valve is not suitable for flow adjustment, but it is suitable for occasions that require fast opening and closing, which is convenient for emergency shutdown of accidents; usually in strict sealing performance, wear, necking passage, rapid opening and closing action, high pressure cut-off (large pressure difference), In pipelines with low noise, vaporization, small operating torque, and small fluid resistance, ball valves are recommended.
The ball valve is suitable for light structure, low pressure cut-off, and corrosive media; the ball valve is also the most ideal valve for low temperature and cryogenic media. For the piping system and device of low temperature media, low temperature ball valve with bonnet should be selected;
When selecting a floating ball valve, its seat material should bear the load of the ball and working medium. Large-diameter ball valves require greater force during operation. Worm gear transmission should be used for ball valves with DN≥200mm; fixed ball valves are suitable for larger diameters. And high pressure occasions; In addition, the ball valve used in the process of highly toxic materials and combustible medium pipelines should have a fire-proof and anti-static structure.
2. Check valve selection instructions
Check valves are generally suitable for clean media, not for media containing solid particles and high viscosity. When ≤40mm, lift check valve should be used (only allowed to be installed on horizontal pipeline); when DN=50~400mm, swing check valve should be used (can be installed on both horizontal and vertical pipelines, such as Installed on a vertical pipeline, the flow direction of the medium should be from bottom to top);
When DN≥450mm, buffer check valve should be used; when DN=100~400mm, wafer check valve can also be used; swing check valve can be made into a very high working pressure, PN can reach 42MPa, It can be applied to any working medium and any working temperature range according to the different materials of the shell and the sealing parts.
The medium is water, steam, gas, corrosive medium, oil, medicine, etc. The working temperature range of the medium is between -196~800℃.
3. Instructions for selection of globe valve
The stop valve is suitable for pipelines that do not require strict fluid resistance, that is, pipelines or devices with high temperature and high pressure medium that do not consider pressure loss, and are suitable for medium pipelines such as steam with DN<200mm;
The stop valve has flow adjustment or pressure adjustment, but the adjustment accuracy is not high, and the pipe diameter is relatively small, it is better to use a stop valve or a throttle valve;
For highly toxic media, a bellows-sealed globe valve should be used; however, the globe valve should not be used for media with high viscosity and media containing particles that are easy to precipitate, nor should it be used as a vent valve or low vacuum system valve.
4. Diaphragm valve selection instructions
Diaphragm valve is suitable for oil, water, acidic medium and medium containing suspended solids whose working temperature is less than 200℃ and pressure is less than 1.0MPa. It is not suitable for organic solvent and strong oxidant medium;
Weir diaphragm valves should be selected for abrasive granular media, and the flow characteristics table of weir diaphragm valves should be referred to when selecting weir diaphragm valves; straight-through diaphragm valves should be selected for viscous fluids, cement slurry and sedimentary media; diaphragm valves should not be used for vacuum pipes except for specific requirements Road and vacuum equipment.
5. Description of butterfly valve selection
Butterfly valves are suitable for large diameter (such as DN﹥600mm) and short structure length requirements, as well as occasions where flow adjustment and fast opening and closing requirements are required. They are generally used for water, oil and compression with temperature ≤80℃ and pressure ≤1.0MPa Air and other media; because the butterfly valve has a relatively large pressure loss compared to the gate valve and ball valve, the butterfly valve is suitable for piping systems with less stringent pressure loss requirements.
THE END
This article comes from the Internet, only for learning and communication, no commercial purpose.